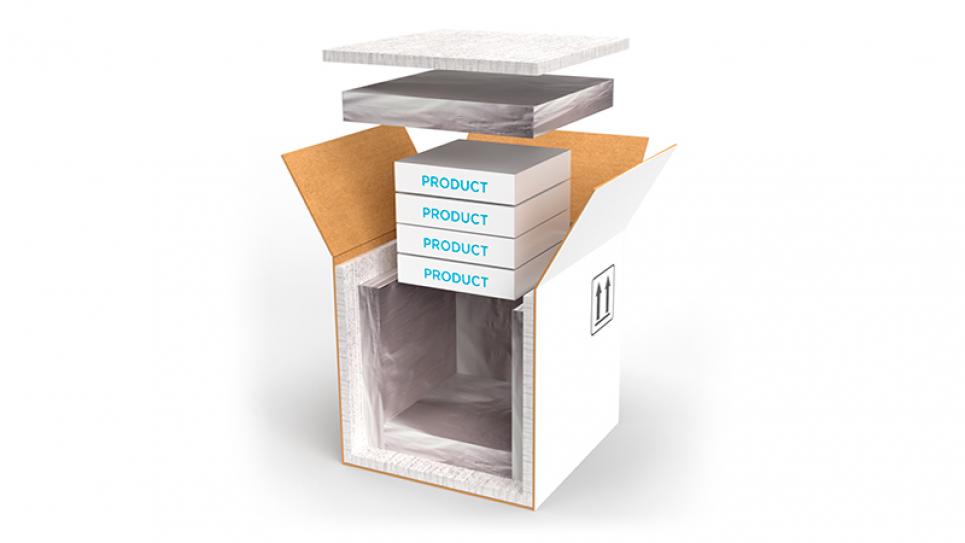
Over the last 20 years, there has been a new regulatory focus on Good Distribution Practices, which prescribe how regulated products should be shipped. Luckily, the emergence of GDP created a strong and capable cold chain just in time to handle the high volume of temperature-controlled vaccine shipments that are required to fight COVID-19.
Pfizer’s vaccine, for example, has storage specifications of -70°C, and is one of the highest profile instances of new challenges facing temperature-controlled distribution. The current distribution channels were not equipped to handle -70°C products. Most distribution centers do not have ultralow temperature freezers and our trucks and planes cannot be kept this cold. This presented a problem for distribution of a vaccine that requires ultra-low conditions.
Pandemic meets ultra-low temperature shipping solution
The answer was found in the thermal shipper.
A thermal shipper is basically a combination of a shipping box and ice chest equipped with cold-packs that keep contents at the correct temperature. Pfizer’s version of this was rather ingenious, with highly efficient vacuum panel insulation and dry ice packs. The shippers also contain a GPS-enabled temperature data logger to track temperatures and location. None of these items are cheap. But given the critical nature of the vaccines, an effective low-temperature shipping container was a necessary innovation.
A fully packed shipper holds almost 5000 doses of vaccine, with price per dose around $20 USD. At $100,000 worth of product in each box, the cost for data loggers, insulation, and cold packs becomes nominal.
However, data loggers can fail, due either to a technical problem with the logger, or human error in deployment. This uncertainty creates the need to qualify the thermal shippers to prove they are fit for their intended use.
Anatomy of a thermal shipper
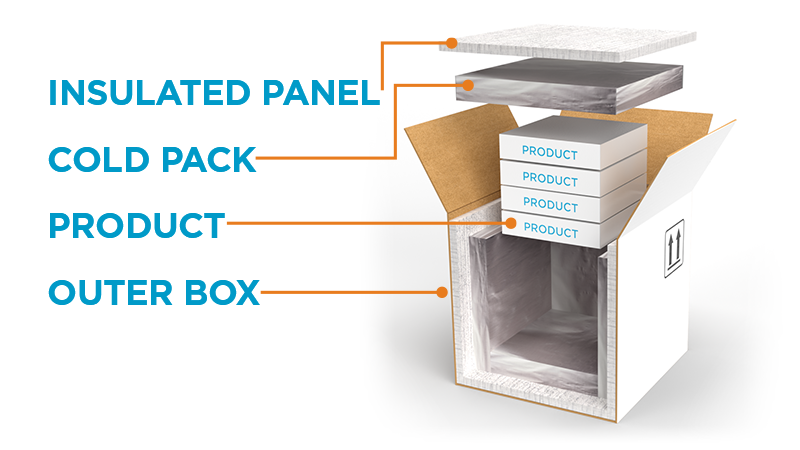
To understand how to qualify a thermal shipper, it is helpful to look its basic anatomy. On the outermost layer, it’s simply a durable cardboard box; usually triple-ply and water-resistant. Because a shipper can cost up to $100 a piece, the boxes must tough so they can be reused.
The next layer is insulation. In our diagram, these are the white panels. For a normal frozen shipment, this would just be polystyrene foam. For an ultralow temperature shipment, Pfizer relied on vacuum insulated panels.
The next layer contains cold packs. In our diagram, these are the silver panels. For a normal frozen shipment, this would be a cold pack of some alcohol mixture engineered to have a phase change (to change from solid to liquid) at the product’s target temperature. The phase change temperature matters, because the cold pack will remain at the phase change temperature until the phase change is complete. For instance, regular old ice packs have a phase change at 0°C, and the temperature gets no warmer until all the ice has melted. For Pfizer’s ultralow temperature shipper, the cold packs are made of dry ice, which changes phase from solid to gas at -78°C.
The innermost layer of the shipper contains the product boxes. Note that the actual product occupies only a small percentage of the available space. As a rule of thumb, a well-designed thermal shipper for conventional frozen shipments will generally have less than 20% of its volume available for product.
Qualification: Proving it works
Validation proves that a process achieves its intended result. Qualification is the term used when validating a piece of equipment. So, at the same time, when we are qualifying the thermal shipper, we are also validating the standard operating procedure for packing the shipper.
To illustrate a qualification process, imagine a shipper meant to transport a frozen product on a four-day trip during summer. The product’s allowable temperature range is between -10°C to -30°C.
Begin by assembling the thermal shipper according to the SOP. The SOP will include specifications, such as the type of cold pack and the conditioning time and temperature required for the cold pack prior to assembly. Place the conditioned cold-packs and load the product containers with a conditioned placebo product. Next, because we are qualifying the shipper, we will add temperature sensors to the product area. Remember, space is at a premium in these boxes; so rather than placing entire data loggers in the box, remote probes on cables will be used. A thermistor probe is a good choice for this application as they are small and accurate, and are available in different operating ranges, and calibrated measurement ranges. A good example is the Vaisala VL-1416, rather than a data logger with internal sensors, like the Vaisala VL-1000.
The key to shipper qualification is to pack the box following the SOP as if it was an actual shipment. The only changes are that the product is a placebo, and that we included temperature sensors in the load.
Place the packed shipper in an environmental chamber that can simulate the temperatures that can be experienced during shipping. Since we are simulating a summer shipment in an unrefrigerated truck, we might set the chamber to 40°C for 12 hours to represent a sunny day, and ramp it down to 15°C for night. Repeat this cycle for four days to simulate a four-day shipment.
After this four-day challenge in the environmental chamber, review the temperature data from the data loggers. Note whether the sensors in the placebo product stayed within temperature specifications (-10°C to -30°C) for all four days. If that was the case, you can have confidence that the thermal shipper, when packed according to the packing SOP, can keep the product within specifications over a four-day trip during the summer with maximum daytime temperatures of 40°C. One study is not enough, so the process is repeated for two more four-day cycles. With three successful results, the thermal shipper is qualified.
The choice of test duration and challenge temperatures is made based on the intended shipping routes and analysis of expected weather patterns. You may need to qualify one thermal shipper and SOP for the summer, and another different shipper and SOP for the winter.
Qualification gives confidence
The end result of a qualified shipper is confidence that the product will be at the right temperature during shipment. Even with an on-board temperature sensor, Pfizer still needed to have a qualified shipper. They had to prove that their single sensor accurately represented the conditions of the entire product area. They also needed confidence that the shipper could maintain the needed temperatures if the on-board sensor failed or the data was lost. In a more conventional scenario with a less critical product, qualifying a shipper can allow distribution with less monitoring. Instead of monitoring the temperature of the shipment with expensive loggers, we can check weather forecasts and make sure shipments arrive within their qualified time limits.
The focus on Good Distribution Practices has provided a more robust cold chain and new technologies have emerged to support it. Many shipments can now be directly monitored with inexpensive and disposable data loggers, that while low on accuracy, are still good enough for this application. However, the fundamentals of shipping time and temperature sensitive products have not changed. We saw this without a doubt with the development of Pfizer’s thermal shipper.
The very low temperature COVID-19 vaccines are a great example of the role of qualification of thermal shippers and its continued relevance. In the case of Pfizer, even though they included GPS-enabled temperature sensors in the shippers, qualification was still necessary. They needed to prove the shipper’s effectiveness in the case that a temperature sensor malfunctioned. Qualification gave confidence that the thermal shipper was properly designed. They needed to have confidence that their packaging SOPs were appropriate for the intended use and that their procedures for recharging the dry ice were effective.
In Europe, CSafe Global developed the thermal shipper used with the Pfizer/BioNtech vaccine. For more information about the CSafe design, here is a short article on their shipper.
“CSafe Global Providing Thermal Protection for COVID-19 Vaccine Shipments from BioNTech Facility”
View our Vaisala Monitoring Products here